The air compressor motor serves as the foundation of any compressor system. After all, it’s tasked with harnessing the electrical energy into the mechanical energy required to get the compressor running. Hence, it could be said this motor is the engine that keeps an air compressor ticking – an indispensable component and its beating heart.
The core of your typical air compressor motor is the induction motor, which is comprised of two elements – the stator and the rotor. The stator looks like its namesake; stationary, usually made from copper or aluminum, and home to the magnets and windings, essential components in activating a magnetic field. On the other hand, the rotor is made of either steel or aluminum and rotates within the stator, hosting the armature that adds electrical current to the equation.
No matter what kind of air compressor is employed, the size of its motor relies on the size of the compressor. Specifically, the larger the compressor, the bigger and stronger the motor must be in order to generate sufficient power. Additionally, it should be noted that this size is dependent upon the particular air compressor being operated – rotary screw compressors needing motors larger than their reciprocating counterparts.
When selecting an air compressor motor, looking at its power rating is important. It indicates the motor’s capacity to deliver power, typically gauged in horsepower (HP). The greater the HP, the more powerful the engine is. Likewise, its efficiency rating should be examined. This reflects how effectively it utilizes electricity, usually expressed as a percentage. The higher the percentage, the more efficient the motor is.
For applications that require a hushed operating volume, induction motors have proven to be an ideal solution, especially for use indoors. Nonetheless, they can’t match the power and efficiency of other motor types due to their emphasis on noise reduction. Therefore, it’s important to consider the applicable needs prior to selecting a motor for a compressor.
The motor of an air compressor should be kept as clean as possible to prevent dirt and other particles from impacting its overall performance. Additionally, it is beneficial to revisit the status of its wiring from time to time to ensure it is adequately intact and that any connections are completely secure. This efficient maintenance will aid in keeping the motor running optimally.
Ultimately, the motor of an air compressor is an indispensable part. This helps to transform and use electrical energy so that the compressor can rightfully do its job. If the incorrect size or power rating is adopted, it could explicitly compromise the operation of the ultimate task. Moreover, to make sure that it remains in prime condition and meets efficiency standards, routine upkeep should always be performed on the motor.
A workhorse of countless industries, the air compressor motor has become a staple of many projects and tools. Boasting a variety from small, handheld units to hefty industrial designs, these motors can be propelled by energy sources such as electric or gasoline. In construction, automotive, and manufacturing – just to name a few – these motors prove to be an invaluable asset in delivering reliable performance.
At the center of an air compressor lies a revolving set of cylinders which are connected to an axle. The rotation of the axle causes the cylinders to compress air, inserting it through a range of ducts and hoses that will eventually lead to the device or tool in need of its power. This compression of air is what supplies the force for the required task.
Two major elements underpin the power output of an air compressor motor; size and fuel used. As a general rule, larger motors will deliver more punch than smaller units. When it comes to fuel type, gas-fuelled motors are a popular choice, however electric motors are often seen to be more efficient and require less upkeep. Despite electric motors providing more power, they come with the cost of needing to keep them in check with regular maintenance.
Choosing the right air compressor motor is crucial for powering the desired tool or appliance. Different tools require different wattage outputs, so it is important that the motor can generate enough juice to effectively operate the device. Luckily, there are many engine models available, such as single stage, two stage, and three stage motors – with those models in ascending sequence of power capabilities and features. Usually, single stage models are the least powerful and offer fewer features; however, two and three stage engines can provide the higher pressures necessary for some machines.
Air compressor motors are used everywhere from powering air tools and painting equipment to many more applications. Essential in many industries, they need to be reliable and bring long term effectiveness. When shopping for an ideal model, you need to consider aspects such as size, power output, and fuel type to see what best fits the requirements of the application.
When it comes to finding the ideal air compressor motor for a given industry, there are three essential factors to weigh: size, power output, and fuel type. Making the accurate selection will prove invaluable in ensuring optimal results. Take the time to properly evaluate these properties and you’ll be rewarded with the perfect motor for your needs.
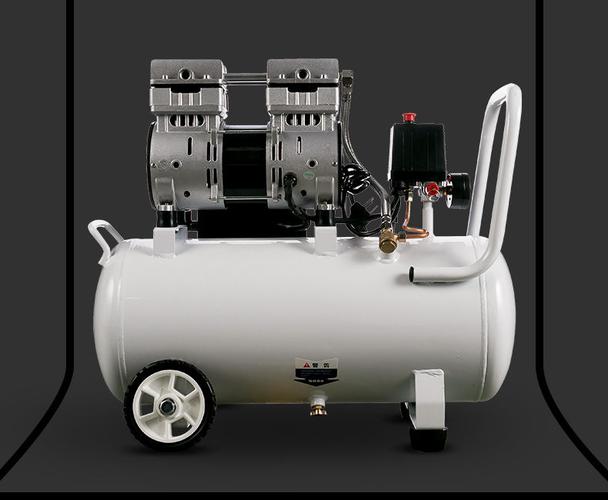
Post time: 2023-08-09