The functioning of an air compressor system relies, in part, on air compressor gauges. By providing key details about the performance of the compressor, they enable users to quickly determine whether it is running as it should. This article dives into the different variations of air compressor gauges, their roles in the system, and how to decipher them.
Air Compressors require two important readings: pressure readings and temperature readings. Pressure gauges are responsible for relaying data on the air pressure, while temperature gauges provide insight into the air’s temperature. Both of these measurements allow individuals to understand the state of the compressor, as well as anticipate future problems or maintain it optimally.
Measuring the internal air pressure is one of the most typical applications of pressure gauges in air compressors. These gauges can usually be spotted as dials that show the current pressure values in either psi (pounds per square inch) or bars. Even with the modern technology, these trusty instruments remain a go-to tool for many technicians.
Reliable temperature readings are provided by utilizing temperature gauges, usually composed of a circular dial that accurately denotes the ambient temperature. Celsius or Fahrenheit is often used to measure the ambient compression air temperature, depending on the settings of the respective gauge.
To accurately interpret the figure on an air compressor gauge, one must take into account the baseline atmospheric pressure. For instance, if the external pressure is measured at 14.7 psi, then a figure of 15 psi on the compressor’s gauge reveals that there is an increase in air pressure within the machinery.
Alongside pressure and temperature readouts, many air compressors also incorporate additional gauge systems to monitor oil pressure, vacuum traction, and airflow pattern.
Oil pressure gauges play a vital role in monitoring the pressure of oil found within a compressor. It enables individuals to ascertain whether the system provides an adequate quantity of oil and can pinpoint its pressure by indicating either psi or bar readings. Essentially, these instruments enable users to keep track of oil levels and determine if any adjustments are needed.
Vacuum gauges are vital instruments which assess the level of vacuum inside a compressor. They provide valuable insight into its operation and help determine if air is being drawn in correctly. Readings are usually quantified in two traditional metrics: either inches of mercury (inHg) or millimeters of mercury (mmHg). Using such information, the performance and efficacy of the compressor can be carefully monitored.
By making use of a flow rate gauge, the rate of air going through the compressor can be calculated. It serves to determine the amount of air generated by the compressor to ensure that an adequate amount is being moved. Generally speaking, readings are usually measured in cubic feet per minute (cfm) or liters per minute (LPM).
A routine checkup of air compressor gauges is essential for guaranteeing that they continue to be in optimum condition. We need to be vigilant for any signs of tear and wear, and any component that holds on to defects should be replaced with haste.
All in all, air compressor gauges are truly indispensable when it comes to compressor systems. These handy tools supply vital details about the machine’s productivity, enabling its operators to ensure everything is functioning optimally. The two most common gauges are the pressure and temperature varieties, though various other kinds may also be included, like oil pressure, vacuum, and flow rate. To guarantee that gauges are running smoothly, it is important that they are periodically checked and maintained.
The air compressor gauge is vital for any air compressor. Acting as a pressure-measuring device, it gives a precise indication of system performance, enabling the compressor to remain in optimal condition. It is such a reliable gauge that it can be used to monitor the performance of any air compressor precisely.
In order to measure the pressure of a system, air compressors require gauges crafted in a variety of shapes and sizes. The most popular of these is the dial gauge – with a needle that traces over a range of numbers to showcase the pressure. Digital gauges offer an alternate way to measure this data – changing the pressure into numerical form for readability, while analog displays illustrate this same element with graphical images.
When shopping for an air compressor gauge, take into account the dimensions of the compressor, the kind of air being compressed, the level of accuracy wanted, as well as the environment in which the gauge will be working in. For instance, a gauge designed for use in colder tempatures might not provide effective performance if it is used in a much more searing climate.
Taking the time to correctly install and use your air compressor gauge is a must, but don’t forget to check in with it periodically. Give it an accuracy reading every once in a while by taking a measurement on the gauge and matching it up against a trusty reference pressure. That way, you’ll have the assurance that your readings are reliable.
The gauge on an air compressor must be treated with respect. If the pressure surpasses the maximum rating of the gauge, harm can be caused, not just to the gauge but also to the compressor. Moreover, unless in use, the gauge should not stay connected to the system as pressure alterations can render it useless or defective.
To help ensure that an air compressed system is performing at its best, an air compressor gauge can be employed. This instrument serves as a monitor to track the system pressure, allowing the user to determine if the system is running as optimum level. Doing so is important and can help to protect against issues while also prolonging the system’s life.
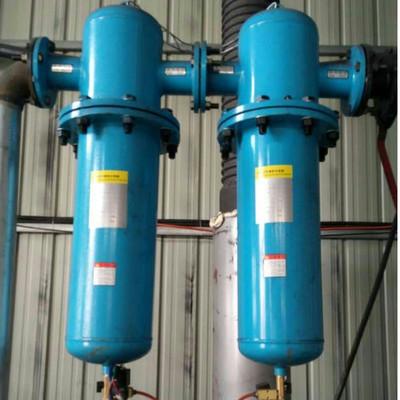
Post time: 2023-07-24